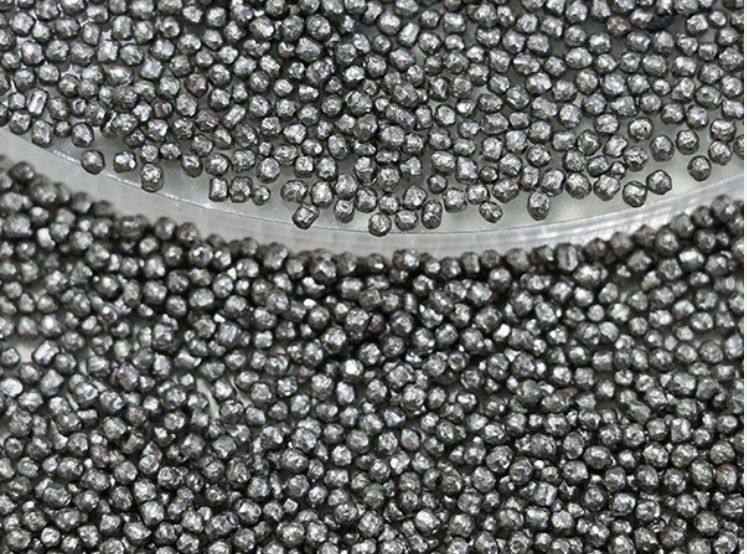
What Are Metal Abrasives?
Metal abrasives consist of small, hard particles made primarily from iron, steel, stainless steel, or other metal alloys. They are manufactured into various forms—such as shots, grits, or powders—depending on the intended application. Due to their durability and hardness, metal abrasives are commonly used in abrasive blasting (also known as sandblasting or shot blasting) to clean and prepare metal surfaces.
Unlike conventional abrasives like sand or glass beads, metal abrasives provide superior impact and cutting action, making them effective for heavy-duty cleaning and surface profiling.
Types of Metal Abrasives
There are several common types of metal abrasives, each suited for specific tasks:
1. Steel Shot
Steel shot consists of spherical steel pellets used primarily in shot blasting machines. It is excellent for removing rust, mill scale, and old paint from steel surfaces while producing a clean, uniform finish. The round shape results in a peening effect that can increase the strength of metal surfaces.
2. Steel Grit
Unlike shot, steel grit is angular and irregularly shaped. It provides a more aggressive cleaning action, ideal for roughening surfaces to improve paint or coating adhesion. Steel grit is often used when a deeper surface profile is needed.
3. Stainless Steel Shot and Grit
These abrasives are corrosion-resistant, making them suitable for cleaning stainless steel or other corrosion-sensitive metals. They leave minimal contamination and maintain the integrity of the metal surface.
4. Copper and Brass Abrasives
Copper and brass abrasives are softer metal abrasives used in specialized applications where minimal damage or surface alteration is required, such as cleaning delicate machinery parts or creating smooth finishes.
Applications of Metal Abrasives
Metal abrasives are widely used in industries such as automotive, shipbuilding, construction, aerospace, and manufacturing for a variety of tasks:
• Surface Cleaning: Removing rust, scale, dirt, and old coatings from metal surfaces before painting or coating.
• Surface Profiling: Creating a rough texture on metal surfaces to improve adhesion of paints, coatings, or adhesives.
• Shot Peening: Strengthening metal components by inducing compressive stress on the surface, enhancing fatigue resistance.
• Deburring: Removing sharp edges or burrs from metal parts after machining.
• Polishing and Finishing: Achieving a smooth or matte finish on metal surfaces.
Advantages of Using Metal Abrasives
• Durability and Reusability: Metal abrasives, especially steel shot and grit, can be reused multiple times, reducing operational costs.
• Efficient Cleaning and Profiling: Their hardness and shape enable effective removal of tough contaminants and the creation of desired surface textures.
• Consistent Performance: Metal abrasives provide uniform cleaning and profiling results, essential for quality control in manufacturing.
• Environmentally Friendly: Unlike some sand-based abrasives, metal abrasives generate less dust and can often be recycled within blasting systems.
• Peening Effect: Steel shot imparts beneficial surface compressive stresses that improve the mechanical properties of metals.
Choosing the Right Metal Abrasive
Selecting the appropriate metal abrasive depends on:
• Type of Surface: For delicate surfaces, softer abrasives like brass are preferred. For heavy-duty cleaning, steel shot or grit is ideal.
• Desired Finish: Angular abrasives (grit) provide rougher profiles; spherical abrasives (shot) offer smoother finishes.
• Equipment Used: Compatibility with blasting machines or grinding equipment should be verified.
• Material to be Cleaned: Stainless steel surfaces require stainless steel abrasives to avoid contamination.
• Environmental and Safety Considerations: Consider dust control and worker protection measures.
Safety and Environmental Considerations
Working with metal abrasives involves exposure to dust, noise, and flying particles. Proper protective gear such as respirators, ear protection, and safety goggles is essential. Additionally, many modern abrasive blasting systems are enclosed or use vacuum collection to reduce environmental impact and improve operator safety.
Recycling and reusing metal abrasives minimize waste and lower costs, making the process more sustainable.Visit our website https://www.master-abrasive.com/ for more details.
Conclusion
Metal abrasives are indispensable in modern industrial surface preparation and finishing. Their strength, versatility, and reusability make them ideal for cleaning, profiling, peening, and polishing metal surfaces across various sectors. Understanding the types and applications of metal abrasives can help industries achieve superior surface quality, improve product durability, and maintain efficient operations.
By choosing the right abrasive type and following best practices in safety and environmental management, users can maximize the benefits of metal abrasives while minimizing risks and costs.